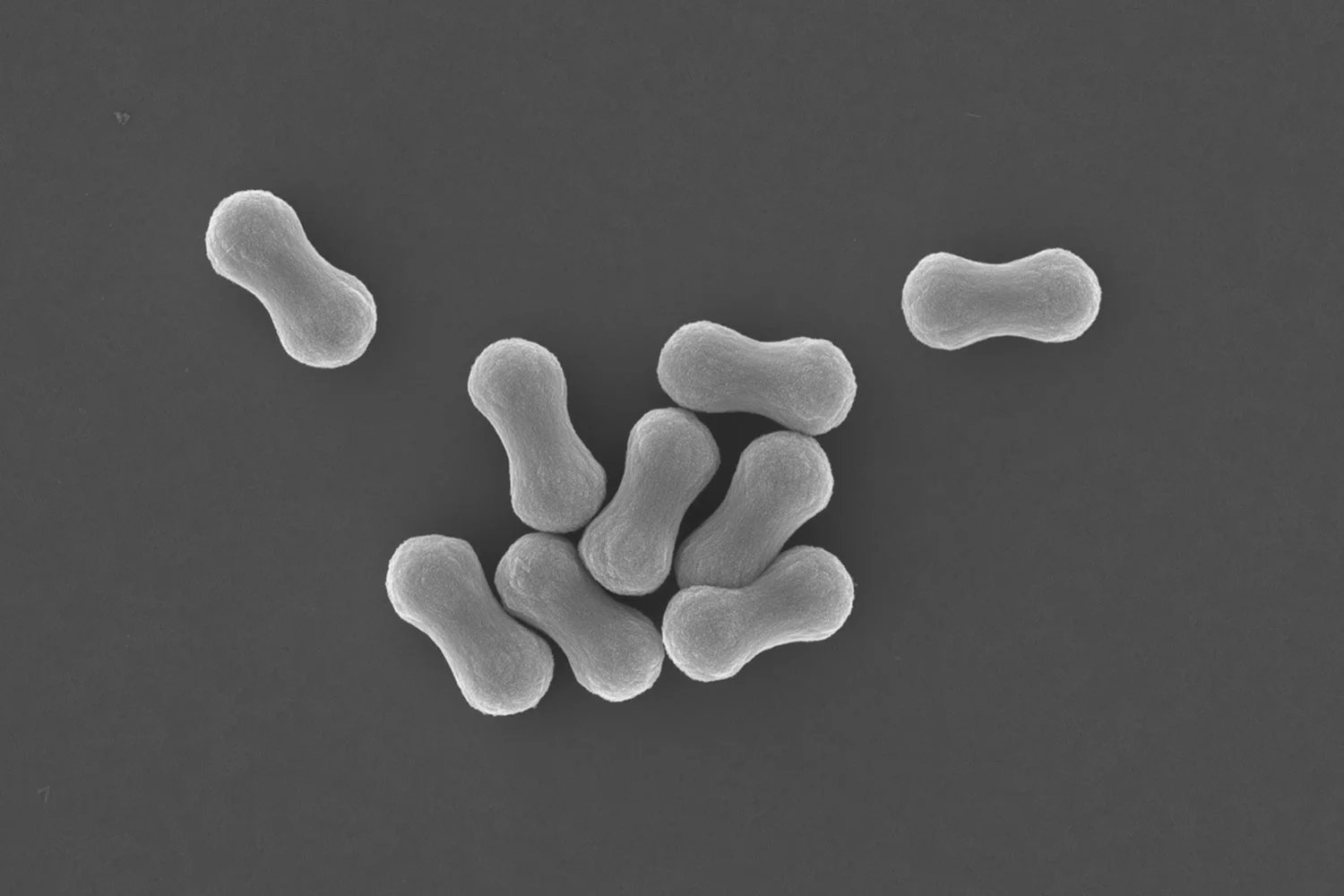
BONLAB BLOG
Thoughts
&
Scientific Fiction
Warwick Researchers Lead the Way in Developing Sustainable Alternatives to Plastics
Researchers at The University of Warwick have made significant progress in the search for sustainable alternatives to conventional plastics. In response to growing environmental concerns, the move towards a circular economy and changing consumer preferences, the research team has identified that certain mixtures of small organic molecules form interesting glasses and viscous liquids. These so-called organic eutectics are promising candidates for replacing polymers in various products.
Researchers at The University of Warwick have made significant progress in the search for sustainable alternatives to conventional plastics. In response to growing environmental concerns, the move towards a circular economy and changing consumer preferences, the research team has identified that certain mixtures of small organic molecules form interesting glasses and viscous liquids. These so-called organic eutectics are promising candidates for replacing polymers in various products.
Plastics have long been a mainstay in modern manufacturing, but their environmental impact has increased demand for eco-friendly alternatives. The Warwick research highlights eutectic molecular glasses and liquids—materials formed by mixing crystalline components—as underexplored yet highly promising options for this purpose.
The team successfully developed a series of hydrophobic eutectic molecular liquids and glasses, each carefully crafted by combining different crystalline components. Using advanced techniques like differential scanning calorimetry (DSC) and UV-vis spectroscopy, the eutectic compositions were precisely determined. The analysis was refined using a trained partial least squares regression model, ensuring accuracy in identifying the optimal material blends.
Fibers can be pulled from the hydrophobic small-molecule eutectic material. It can also be molded into shapes, glass-blown into baubles, or cast as flexible films.
One key challenge in creating sustainable plastic alternatives is ensuring long-term stability. The Warwick team addressed this by testing the amorphous materials over an extended period of up to 14 months, using powder X-ray diffraction (PXRD) to confirm their resistance to crystallization. This durability is crucial for ensuring that products maintain their integrity throughout their shelf life.
In addition to stability, the researchers investigated the processability of these materials by examining their rheological properties. They found that all the liquids exhibited low fragility indices, making them suitable for various manufacturing processes, including glassblowing, fiber pulling, film formation, and molding. Importantly, the team demonstrated that the properties of these materials could be tailored to specific applications by blending different eutectic systems or incorporating plasticizers.
Prof. dr. ir. Stefan Bon, lead investigator of the work, says: “The original plan was to develop an anything-but-plastic concept material for the formulation industry. Dr. Joshua Ryan, a talented former PhD researcher in my team, BonLab, undertook a systematic study of blending small hydrophobic organic molecules that could undergo a variety of non-covalent interactions with one another. That these hydrophobic eutectic systems had such remarkable physical properties, was beyond our initial expectations. We brought our colleague Prof. Gabriele Sosso on board to study by computer simulations how these eutectic mixtures interacted on a molecular level. These small molecule organic eutectic systems offer an opportunity to further develop high-performance materials that can replace conventional polymers in various applications. In a way, they can be seen as a non-covalent analogue to dynamic reversible macromolecular covalent materials, known as vitrimers.”
To showcase the practical potential of these materials, the researchers conducted a controlled release study using a eutectic system composed of 4-hydroxychalcone and bifonazole as a matrix. This study serves as a proof-of-concept, highlighting the versatility of eutectic materials in applications such as drug delivery and beyond.
The University of Warwick's groundbreaking research, published open access in Chemical Science, the flagship journal of the Royal Society of Chemistry, opens new avenues for developing sustainable, versatile alternatives to traditional plastics. As legislative changes and consumer preferences continue to push for greener solutions, these innovative organic materials offer a promising path forward.
ENDS
The scientific paper entitled “Small molecule organic eutectics as candidates to replace plastics.” published in Chemical Science can be accessed at: https://doi.org/10.1039/D4SC02574A
For more information on BonLab, see https://bonlab.info
For more information, please contact the University of Warwick press office at press@warwick.ac.uk or phone 07392 125 605
Water-based nanocapsule dispersions for tuneable energy storage
Phase change materials, also known as PCMs, can capture, store, and release energy when they undergo a phase transition. One class of PCMs with relatively high latent energy storage capabilities are alkane-based waxes. These store energy upon melting and will release it again when they solidify through crystallization. To make use of this so-called latent heat is helpful for many applications, and indeed can be found, for example, in building insulation and temperature regulation materials. If, however, we would like to use this concept in a temperature-regulating fluid, we need to disperse the PCMs into a liquid, such as water, that in itself has a high heat capacity and thus the ability to store energy.
Phase change materials, also known as PCMs, can capture, store, and release energy when they undergo a phase transition. One class of PCMs with relatively high latent energy storage capabilities are alkane-based waxes. These store energy upon melting and will release it again when they solidify through crystallization. To make use of this so-called latent heat is helpful for many applications, and indeed can be found, for example, in building insulation and temperature regulation materials. If, however, we would like to use this concept in a temperature-regulating fluid, we need to disperse the PCMs into a liquid, such as water, that in itself has a high heat capacity and thus the ability to store energy.
Creating a dispersion of PCMs is a complex task that presents an intellectual challenge. If we were to emulsify molten wax using ordinary surfactants into droplets dispersed in water, a problem would arise upon cooling. When certain wax droplets crystallize, these will touch other droplets in their vicinity triggering crystal growth and fusion of the droplets. The emulsion is destabilized and, upon heating, will not return to its original state. This complexity underscores the urgent need for innovative solutions in the field of materials science.
The solution to this challenge is to encapsulate the wax. This involves surrounding the wax droplets with a protective shell that prevents fusion. However, a new problem arises when the capsules are large, such as in the micron length scale or upwards. In these cases, the capsules can still jam together and obstruct the flow of the liquid. To overcome this, we need to miniaturize the entire system and fabricate wax nanocapsules that remain colloidally stable throughout their application. This approach not only solves the problem but also allows us to blend nanocapsules containing different waxes, thereby tuning the energy storage characteristics.
Our paper recently published in the Royal Society of Chemistry journal Polymer Chemistry and entitled: “Phase change material nanocapsules for latent function thermal fluids with tuneable thermal energy storage profiles” does exactly that.
We prepared mini-emulsions, which are stable tiny droplets of various methacrylates in the presence of trimethylolpropane trimethacrylate (TMA) as a crosslinker, and n-hexadecane (HD), n-octadecane (OCT), and n-docosane (DOC) as PCM. One important aspect was to use an ω-unsaturated poly(n-butyl methacrylate-b-[(methacrylic acid)-co-(methyl methacrylate)]) macromonomer as a reactive macromolecular emulsifier, to secure colloidal stability of our nanocapsule systems. The performance of a thermal fluid of DOC nanocapsules was tested against water, with promising results. As a tunability concept, crosslinked poly(methyl methacrylate) nanocapsules of n-octadecane (OCT) and n-docosane (DOC) were blended as a tuneable latent function thermal fluid.
You can read the paper here:
Templating Calcium Phosphate onto Graphene Oxide Sheets
Single-layer graphene oxide sheets are interesting as a flexible 2D material, with xy-dimensions variable up to a centimetre in length and a z-thickness of a single carbon atom. The presence of oxygen atoms with functional groups, such as hydroxy, epoxy, carboxylic acid, ketone, or aldehyde, provides graphene oxide (GO) with polarity. This unique property allows GO to disperse as single sheets in polar solvents like water or DMSO at low concentrations, in the absence of electrolytes or other colloidal particles.
Single-layer graphene oxide sheets are interesting as a flexible 2D material, with xy-dimensions variable up to a centimetre in length and a z-thickness of a single carbon atom. The presence of oxygen atoms with functional groups, such as hydroxy, epoxy, carboxylic acid, ketone, or aldehyde, provides graphene oxide (GO) with polarity. This unique property allows GO to disperse as single sheets in polar solvents like water or DMSO at low concentrations, in the absence of electrolytes or other colloidal particles.
Our recent findings, published in RSC Polymer Chemistry (https://doi.org/10.1039/D4PY00300D), have shown that grafting polymer chains from the surface of GO significantly enhances its dispersion. This is particularly true when the polymer chains are of a branched chain architecture. The grafted branched polymer chains provide additional electrostatic and steric stabilization against sheet stacking and crumpling, a discovery that could have significant implications in the field of materials science.
SEM images of single graphene oxide sheets that are decorated with a layer of calcium phosphate, deposited to a templated synthesis route.
The 2D architecture of single GO sheets dispersed in water is an exciting template for depositing inorganic materials, especially now that the grafted polymer chains can be engineered to withstand the ionic precursor concentrations so that the sheets remain dispersed and can additionally serve as crystal nucleation sites.
In our paper published in the Journal of Colloid and Interface Science we show that it is possible to grow Calcium Phosphate onto single dispersed sheets of GO in water. The work was led by former PhD researcher dr. Wai Hin Lee.
Prof. dr. ir. Stefan Bon says: “This paper shows that as a result of the grafted branched polymer, the use of dispersed Graphene Oxide sheets as a template for mineralization is now possible and straightforward. It opens up all sorts of possibilities for hybrid material design”
You can read the paper here: https://doi.org/10.1016/j.jcis.2024.06.221