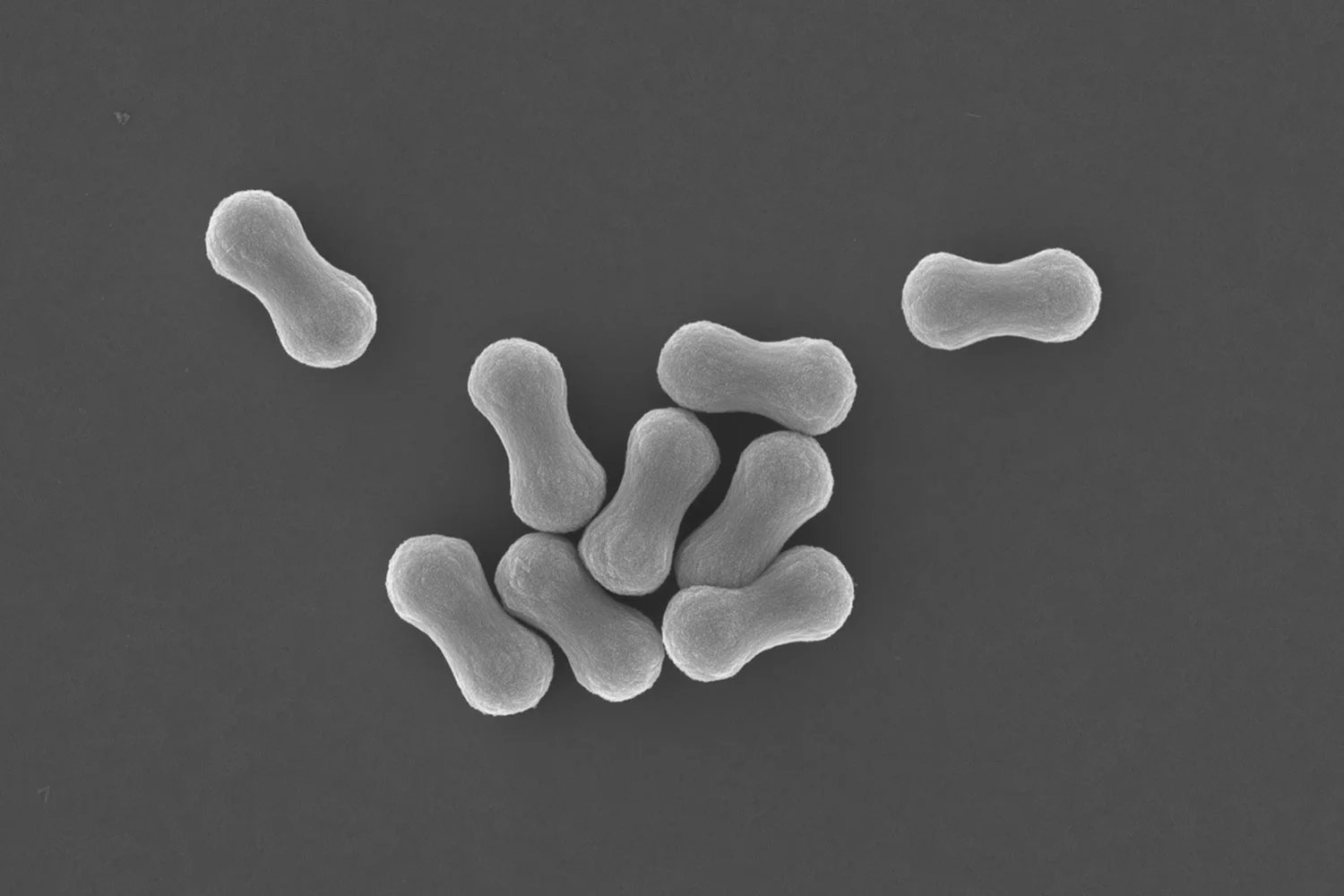
BONLAB BLOG
Thoughts
&
Scientific Fiction
BonLab fabricates textured microcapsules through crystallization
Watch the Talk by clicking here.
Microcapsules can be found in a range of commercial applications, including cosmetics, healthcare, agriculture, and food. The capsules serve as a storage vessel for an active ingredient, for example a nutrient or fragrance. They can have a variety of designs, the simplest form being a single internal liquid-based core surrounded by a solid shell. The chemical and physical characteristics of this shell influence the colloidal stability of capsules in formulations, dictate the permeability and mechanical robustness of the capsules, and can potentially regulate substrate adhesion. Beside storage, these features of the microcapsules are there to regulate and control release and delivery of the active compound.
A considerable part of the technologies used to produce microcapsule relies on the use of synthetic polymers that do not break down, with terrible consequences for environmental build up. One way is to make use of biocompatible and degradable plastics.
We provide an alternative solution, in that we fabricate the capsule from small molecular compounds, instead of polymers, that can crystallize.
Microcapsules can be found in a range of commercial applications, including cosmetics, healthcare, agriculture, and food. The capsules serve as a storage vessel for an active ingredient, for example a nutrient or fragrance. They can have a variety of designs, the simplest form being a single internal liquid-based core surrounded by a solid shell. The chemical and physical characteristics of this shell influence the colloidal stability of capsules in formulations, dictate the permeability and mechanical robustness of the capsules, and can potentially regulate substrate adhesion. Beside storage, these features of the microcapsules are there to regulate and control release and delivery of the active compound.
A considerable part of the technologies used to produce microcapsule relies on the use of synthetic polymers that do not break down, with terrible consequences for environmental build up. One way is to make use of biocompatible and degradable plastics.
We provide an alternative solution, in that we fabricate the capsule from small molecular compounds, instead of polymers, that can crystallize.
Artist impression of textured microcapsules made through crystallization.
In our work, published in the scientific journal ACS Applied Materials & Interfaces we focus on the fabrication of microcapsules of which the capsule wall is composed of an inter-locked mesh of needle-like crystals, which besides capsule rigidity and semi-permeability, provides a roughened surface texture.
In this proof-of-concept study crystals of the small organic compound decane-1,10-bis(cyclohexyl carbamate) are formed within the geometric confinement of emulsion droplets, through precipitation from a binary-solvent dispersed phase. This binary mixture consists of a volatile solvent and non-volatile carrier oil. Crystallization is facilitated upon supersaturation due to evaporation of the volatile solvent. We show that the microcapsule diameter can be easily tuned using microfluidics.
The technology is shown to be scalable using conventional mixers, yielding spikey microcapsules with diameters in the range of 10-50 μm. We highlight that the capsule shape can be molded and arrested by jamming using recrystallization in geometric confinement.
With an eye on commercial applications we show that these textured microcapsules show enhanced deposition onto a range of fabric fibers. They outperform their traditional polymeric analogues by sticking better on fibrous substrates.
Prof. dr. ir. Stefan Bon says: “I am delighted with this work, a coordinated effort which was led by first author dr. Sam Wilson-Whitford. A while back we decided in BonLab that our science needed to be greener, and more sustainable. We think our way of making textured microcapsules meets these criteria. We hope that it inspires industry, and that the concept will prove to be useful across a variety of application areas.”
The paper can be accessed here:
https://pubs.acs.org/doi/10.1021/acsami.0c22378
A talk on the topic can be accessed here:
https://www.formulation.org.uk/pc20programme/250-past/2021/pc20/860-pc20-bon.html
What happens to particle size distributions when making reactive surfactants and polymer colloids by emulsion polymerization?
When we synthesize polymer colloids by emulsion polymerization, molecular surfactants are often employed. These are required to keep the polymer latex particles dispersed in the water phase, so that they do not clump together, a phenomenon known as coagulation. Keeping polymer dispersions stable is especially important in end applications, such as waterborne coatings and adhesives.
A downside of the use of surfactant molecules is that they can desorb from the surface of the latex particles. This makes the particles colloidally unstable, and they coagulate. This can be disastrous in product formulations, such as water-based paints which have many components. Another downside of this mobility of the surfactant molecules is that they can migrate in the final coating, once applied on a substrate. This leads to deterioration of the properties of the coated film.
When we synthesize polymer colloids by emulsion polymerization, molecular surfactants are often employed. These are required to keep the polymer latex particles dispersed in the water phase, so that they do not clump together, a phenomenon known as coagulation. Keeping polymer dispersions stable is especially important in end applications, such as waterborne coatings and adhesives.
A downside of the use of surfactant molecules is that they can desorb from the surface of the latex particles. This makes the particles colloidally unstable, and they coagulate. This can be disastrous in product formulations, such as water-based paints which have many components. Another downside of this mobility of the surfactant molecules is that they can migrate in the final coating, once applied on a substrate. This leads to deterioration of the properties of the coated film.
A solution to these problems is to use reactive surfactants. These have the ability to attach themselves to the latex particles irreversibly, through a covalent chemical bond.
Catalytic chain transfer polymerization (CCTP), a free radical polymerization processs that employs a cobalt catalyst in tiny amounts, is able to make polymer molecules with a reactive unsaturated end group. These macromolecules, also called macromonomers, can be chain extended using a process referred to as RAFT (Reversible Addition Fragmentation chain Transfer), into longer polymer molecules that can behave like surfactant molecules. The reactive end group is preserved, which means that if our polymer reactive surfactant is used in an emulsion polymerization to make latex particles, it will be attached permanently to the latex particles.
The technology to fabricate blockcopolymers under emulsion polymerization conditions using CCTP derived macromonomers, was originally reported in the 1990s by Moad and coworkers. Emphasis has been lying on polymer chain growth and hence the molecular weight distribution.
In our paper published in a special polymer colloids issue of the ACS journal Biomacromolecules PhD students Wai Hin Lee and Joshua Booth investigated the emulsion polymerization processes from a different angle. We investigated the particle size distributions and studied how these developed throughout a three-stage emulsion polymerization process (see the image below).
Three stages of emulsion polymerizations: Catalytic chain transfer emulsion polymerization to make an alkali soluble macromonomer, chain extension to make a reactive block copolymer surfactant, emulsion polymerization to prepare soft polymer colloids using the reactive surfactant.
Firstly, we looked at the catalytic chain transfer emulsion polymerization to make the hydrophilic block of the reactive polymer surfactants. Next we looked at how the particle size distributions changed upon chain extension with a hydrophobic block. Finally, we disintegrated the latex particles into a reactive polymer surfactant micellar dispersion. This was then used to carry out emulsion polymerizations to produce polymer latexes in absence of conventional surfactants.
Prof. dr. ir. Stefan Bon says: “I hope that people like the angle we took in our work, to shine a light on how the latex particles are formed and how the particle size distributions develop. We showed that it was possible to make soft polymer latexes with average particle diameters below 100 nm using our reactive surfactants, easily up to overall solids content of 30wt%. This is an excellent achievement. We believe that the reported emulsion polymerization processes are robust and versatile, and are delighted that we can produce polymer latexes that do not suffer from surfactant migration upon application.”
Details on the paper : https://pubs.acs.org/doi/10.1021/acs.biomac.0c00766
BonLab collaborates to produce bacteria containing biocoatings
We have a long history of making polymer dispersions to be used in waterborne coatings. The polymer colloids, or latex particles, are made by emulsion polymerization. Prof. Joe Keddie from the Physics Department at Surrey University contacted us if we were interested to help out on a bio-coatings project that needed some bespoke polymer latexes and colloidal formulations. With the term bio-coatings we mean here the coating formulation has the ability to entrap metabolically-active bacteria within the dried polymer film.
We loved the concept. In BonLab, PhD student Josh Booth optimized the synthesis of acrylic polymer latexes at approximately 40wt% solids with a monomodal particle size distributions. Important was to use bacteria-friendly surfactants in the semi-batch emulsion polymerization processes. Important was also to have a dry glass transition temperature of the polymer latex binder around 34 ℃, so that film formation could occur at temperatures which preserved viability of the bacteria.
The latexes were formulated as mixtures with halloysite nanoclay (hollow tubes) and E coli bacteria back at Surrey. The tubular clay was introduced to create porosity inside the polymer nanocomposite films. The overall composition of the waterborne formulation was optimized for mechanical and bacterial performance.
We have a long history of making polymer dispersions to be used in waterborne coatings. The polymer colloids, or latex particles, are made by emulsion polymerization. Prof. Joe Keddie from the Physics Department at Surrey University contacted us if we were interested to help out on a bio-coatings project that needed some bespoke polymer latexes and colloidal formulations. With the term bio-coatings we mean here the coating formulation has the ability to entrap metabolically-active bacteria within the dried polymer film.
We loved the concept. In BonLab, PhD student Josh Booth optimized the synthesis of acrylic polymer latexes at approximately 40wt% solids with a monomodal particle size distributions. Important was to use bacteria-friendly surfactants in the semi-batch emulsion polymerization processes. Important was also to have a dry glass transition temperature of the polymer latex binder around 34 ℃, so that film formation could occur at temperatures which preserved viability of the bacteria.
The latexes were formulated as mixtures with halloysite nanoclay (hollow tubes) and E coli bacteria back at Surrey. The tubular clay was introduced to create porosity inside the polymer nanocomposite films. The overall composition of the waterborne formulation was optimized for mechanical and bacterial performance.
Prof. dr. ir. Stefan Bon says: “We are delighted to be part of this study, and are pleased with the outcomes. Credit goes to the teams at the University of Surrey for making it all a success. The concept of biocoatings fits well with the ethos of the BonLab to fabricate materials from colloidal building blocks. We hope to stay involved and work together on next generation advanced coatings, with a green twist”
The paper is published in the ACS Journal Biomacromolecules and shows that large free-standing films of bacteria containing biocoating composites can be made.
The work is a collaborative study with research teams at Surrey University: dr. Yuxiu Chen and prof. Joe Keddie (Soft Matter Group, dept. of Physics), and Simone Krings and dr. Suzanne Hingley-Wilson (dept. of Microbial Sciences).